Schritt für Schritt: die Herstellung einer Sense
Eine Sense entsteht in bis zu 32 Arbeitsschritten. Welche diese sind und wer daran mitarbeitet, erfahren Sie hier.
Über Jahrhunderte entwickelten Schmiede eine große Zahl unterschiedlicher Sensentypen. Sie passten die Form der Sensenblätter an Bodenbeschaffenheit sowie Mähgut und -technik an. Die Kundschaft konnte aus einer großen Vielfalt an Sensenformen auswählen. Kataloge informierten über die jeweiligen Typen und ihre Funktionen. Zur besseren optischen Unterscheidung wurden die Sensen gekennzeichnet.
Herstellerangaben und Produktinformation wurden in die Hamme eingeschlagen. Die Hamme dient zur Befestigung der Sense am Sensenbaum. Die Sensenblätter wurden mit Hilfe von Schablonen beschriftet oder mit Etiketten beklebt.
Die Arbeit des Sensenschmieds
Im Film ist zu sehen, wie im Sensenhammer auf dem Museumsgelände eine Art Sichelrohling unter dem Klepperhammer geschmiedet wird. Der Film dokumentiert die Arbeitsschritte, die ein gelernter Sensenschmied ausführt – und selbst erklärt.
Vorarbeiten
Ablängen
Das angelieferte Stangenmaterial, der Sensenstahl, war meist 4 Meter lang und hatte einen Rechteckquerschnitt von 15 x 35 oder 45 Millimetern. Je nach gewünschter Sensenform wurden die Stangen auf die gewünschte Länge geschnitten. Es entstand der „Bröckel“. Jeder Bröckel ergibt ein Sensenblatt.
Schmieden
Ausrecken zum Zain
Der Bröckel wurde im Feuer auf die Schmiedetemperatur von 950 bis 1000 Grad Celsius erwärmt und dann unter dem Reckhammer ausgereckt, d. h. in die Länge geschmiedet. Der Bröckel hatte nun die gewünschte Länge der zukünftigen Sense und wurde ab jetzt als „Zain“ bezeichnet.
Beim Schmieden wendeten die Schmiede das Werkstück bei jedem Schlag um 90 Grad Celsius hin und her. Das ist der „Wendeschlag“.
Der Sensenschmied hielt das Werkstück mit der Zange fest. Das Stückchen des Stahls, das im Zangenmaul steckte, blieb unbearbeitet. Aus ihm wurde im nächsten Arbeitsschritt die Hamme geschmiedet. Die Hamme dient zur Befestigung der Sense am Sensenbaum, dem Stiel. Der Stahl steckte bis zum Anschlag im Zangenmaul, damit ausreichend Stahl für die Hamme zur Verfügung stand.
Beteiligte Berufe:
- Wärmer, Wärme- oder Ofenjunge: Im Sensenhammer bediente er den Wärmeofen, sorgte für Kohlennachschub und reichte dem Recker oder Reckschmied die Rohlinge an.
- Recker oder Reckschmied
Hammeschmieden
Um die Hamme, das Verbindungsstück zwischen Sensenblatt und Stiel, zu schmieden, wurde das nicht bearbeitete Ende des Zains geglüht und zu einem Streifen ausgeschmiedet. Der Streifen wurde dann abgebogen, so dass er im rechten Winkel zum Zain stand. Beim Biegen entsteht ein Wulst, der glattgeschmiedet werden musste. Die Form der zukünftigen Sense ist schon zu erkennen, jedoch noch sehr grob. Sie wurde vom Warzenmacher verfeinert. Er schmiedete die Hamme gleichmäßig aus. Am Ende der Hamme schmiedetet er den warzenartigen Knopf aus.
Der Knopf, die Warze, diente später dazu, die fertige Sense am Holzstiel, dem Sensenbaum, zu befestigen. Im Sensenbaum gab es das Warzenloch, in das die Warze eingriff. Sense und Holzstiel wurden mit dem Sensenring dann abschließend fest verbunden.
Die geschilderten Arbeitsschritte wurden auch als „Hammenknöpfen“ bezeichnet.
Zum Abschluss dieses Arbeitsschritts wurde das Zain-Ende ausgespitzt, damit beim anschließenden Breiten die Spitze beim Ausformen des Sensenblatts geschmiedet werden konnte.
Beteiligte Berufe:
- Hammenschmied: im Sensenhammer tätiger Schmied, Spezialisierung auf das Ausschmieden der Hamme, dem Griff der Sense
- Warzenmacher: im Sensenhammer tätiger Schmied; Spezialisierung auf das „Knöpfen“ der Hamme. Dafür wird die Hamme gleichmäßig ausgeschmiedet und mit einer Warze versehen, auch Knopf genannt. Die Warze dient der Befestigung am Sensenbaum, der hölzernen Halterung an der Sense.
Breiten
Der Zain wird unter dem Breitehammer zum Sensenblatt ausgeformt. Dieser Arbeitsschritt heißt „Breiten“. Dafür wurden drei Hitzen benötigt, d. h. die Sense musste während des Breitens zweimal zwischengeglüht werden, bis das Sensenblatt seine Rohform hatte. Die Rohform wurde im Arbeitsprozess mit der Mustersense abgeglichen.
Mit der ersten Hitze erfolgte das Langbreiten. Vom Sensenrücken aus wurde das Blatt unter dem Hammer zur Schneide hin mehrmalig durchgezogen, so dass es so ausgedünnt wurde, wie das Muster der gewünschten Sensenform es vorgab. Die Mustersense diente auch als Abgleich für die erforderliche Krümmung.
Nach dem Langbreiten folgte das Bartbreiten. Das hintere Drittel der Sense war die breiteste Stelle des Blattes und wurde als Bart bezeichnet. Beim Bartbreiten wurde diese Stelle in die Breite getrieben. Die Bartbreite ist jeweils spezifisch für ein Sensenmodell und diente daher zur Modellbestimmung. Um das Sensenblatt vor Verbiegen zu schützen, ließ der Breiter am Bart eine schmale Rippe stehen, die stabilisierte.
Mit der dritten Hitze konnte der Breiter das Blatt fertigbreiten. Das gesamte Sensenblatt wurde noch einmal vom Sensenrücken her bearbeitet, so dass die lang- und die bartgebreiteten Stellen angeglichen wurden. Das Blatt hat jetzt eine Stärke von ca. 1 bis 2 Millimetern. Die Rohform war nun endgültig festgelegt.
Das Breiten des Sensenblatts war der wichtigste Arbeitsschritt. Der Schmied, der diese Arbeit ausführte, wurde Breiter genannt. Er musste sehr versiert sein und erhielt den höchsten Lohn im Sensenhammer.
Beteiligte Berufe:
- Breiter: Schmied im Sensenhammer; Spezialisierung auf das Ausschmieden des Sensenblattes, dem wichtigsten Arbeitsschritt bei der Sensenherstellung. Die Aufgabe erfordert ein hohes Maß an Kenntnis und Versiertheit. Der Breiter war bestbezahlter Mitarbeiter im Sensenhammer.
Formgebung
Der Rücken wird aufgestellt
Der Sensenrücken blieb beim Breiten in gleichmäßiger Stärke stehen. Er wurde nun aufgestellt. Der Schmied nutzte dafür entweder seinen Amboss oder eine Aufruckmaschine. Letztere beschleunigte den Arbeitsprozess. Der Sensenrücken verlieh der Sense Stabilität und Biegefestigkeit.
Beteiligte Berufe:
- Aufruckner: Schmied im Sensenhammer; Spezialisierung auf das Aufstellen des Sensenrückens
Glattschmieden, Zuschnitt der Sensenform
Im Anschluss wurden Krümmung und Spitze dem Sensenmuster entsprechend ausgeschmiedet. Das Sensenblatt hatte nun seine endgültige Form. Es wurde abschließend glattgeschmiedet. Der „Abschneider“ schnitt nun mit einer Schere das Blatt dem Sensenmuster entsprechend vom Bart bis zur Spitze zurecht.
Beteiligte Berufe:
- Spitzenformer: Schmied im Sensenhammer; Spezialisierung auf das Ausformen der Sensenspitze
- Abschneider: Schmied im Sensenhammer; Spezialisierung auf das mustergerechte Abschneiden des Sensenblattes
Hamme aufstellen
Die Hamme wurde aufgestellt und in die richtige Stellung gebracht, damit die Sense später problemlos am Sensenbaum befestigt werden konnte. Jeder Sensentyp hatte eine eigene, spezifische Höhen- und Winkelstellung für die Befestigung am Sensenbaum.
Anschließend wurden Sensen- und Markenzeichen in die Hamme eingeschlagen. Jeder Sensenhammer hatte sein eigenes Sensenzeichen. Es wurde auf die Oberseite gesetzt. Die Markenzeichen enthielten Informationen zur Sortenbezeichnung (zum Beispiel Hartstahl) und Längenangaben. Sie wurden auf der Unterseite eingeschlagen.
Beteiligte Berufe:
- Hammenaufsetzer: Schmied im Sensenhammer; Spezialisierung auf das Aufsetzen der Hamme in den gewünschten Winkel. Ursprünglich schwere Handarbeit, weil die Hamme am Ambosshaken angelegt und mit Muskelkraft nach oben gebogen werden musste. Im Lauf des 20. Jahrhunderts wurden Maschinen für diese Arbeit entwickelt. Sie rationalisierten den Arbeitsschritt erheblich.
Das Einschlagen der Zeichen, auch Stempeln genannt, wurde ebenfalls automatisiert. Eine Presse übernahm diese Aufgabe.
Härten
Härten und Anlassen
Das Härten ist nach dem Breiten eine der wichtigsten Aufgaben im Herstellungsprozess einer Sense. Nur durch die richtige Härte wurde die vorgeschriebene Schnittfähigkeit der Sense erzielt. Die Kunst des Härtens war es, dass die Sense weder zu weich noch zu hart war.
Mehrere Sensen wurden in einem Ofen auf etwa 800 Grad Celsius erhitzt. Die Härter mussten die Temperatur anhand der Metallfärbung erkennen. Bei 800 Grad Celsius ist das Metall kirschrot. Dafür brauchten sie nicht nur einen abgedunkelten Raum, sondern auch viel Erfahrung.
Die Härter nahmen die Sensen aus dem Ofen und schreckten sie mit Hilfe einer Tauch- oder Härtezange im Härteöl ab. Das Härteöl hat eine Temperatur von 40 bis 50 Grad Celsius. Damit die Sense überall gleichmäßig und gleichschnell mit dem Härteöl in Kontakt kommt, besteht die Härtezange aus gelochten Backen, die die Sense so zwischen sich fixieren, dass die Sense beim extremen Temperaturwechsel nicht verziehen kann. Sie muss ihre Form beibehalten. Jede Sensenform hatte entsprechend eine eigene Härtezange.
Nach dem Abschrecken war die Sense viel zu hart und musste daher wieder erwärmt werden. Dieser Prozess ist das Anlassen. Die Sense wurde in einem Ofen auf etwa 350 bis 450 Grad Celsius erwärmt. Nun hatte sie die richtige Härte, um die Schnittfähigkeit und Haltbarkeit bei der Anwendung zu gewährleisten.
Verfeinern
Tupfen mit anschließendem Richten
Die gehärteten Sensen mussten nun „verfeinert“ werden. Der Prozess startete in der Richterei. Dort wurden die Sensen auf Fehler wie Wölbungen hin untersucht. Die „Vorrichter“ korrigierten den Sensenrücken und richteten die Sensenspitze.
Nach der Richterei wurden die Sensen unter den schneller laufenden Klipperhämmern (850 Schläge in der Minute) in der Schmiedehalle geglättet, mit der richtigen Wölbung versehen und die Schneide wurde bearbeitet. Die Schmiedearbeit unter dem Klipperhammer diente auch dazu, das Blatt zu egalisieren. Nur ein egalisiertes Sensenblatt konnte poliert werden. Außerdem wurde das Metallgefüge der Sense verdichtet, um die richtige Spannung im Gefüge zu erreichen. Der nächste Arbeitsschritt, das „Grautupfen“, diente demselben Zweck. Ein schnell laufender punktförmiger Hammer erzeugte tupfenartige Schlagspuren auf der Sense. Danach wurde noch einmal gerichtet, das heißt die Stellung der Blätter korrigiert, die Wölbung zwischen Rücken und Schneide nachgespannt, bauchige Stellen ausgeglichen und die richtige Längswölbung zwischen Bart und Spitze erzeugt.
Schleifen
Schleifen
In der Schleiferei wurde die Schneide angeschliffen. Die Schleifer arbeiteten im Stehen und in gebückter Haltung an Schleifsteinen von bis zu 2 Metern Durchmesser. Sie banden sich hölzerne „Schleifschuhe“ vor die Unterschenkel, um die Verletzungsgefahr zu verringern.
Das Sensenblatt wurde gegen den Stein gedrückt. Dabei übte der Schleifer mit den Unterschenkeln Druck auf ein Gestell – den Stößel – aus, dass das Sensenblatt an den Stein drückte. Der Schleifer begradigte die von den vorherigen Arbeitsschritten unebene Klinge. Die Abnehmer, z. B. Bauern, schärften die Klingen dann ihren Bedürfnissen entsprechend durch Dengeln nach.
Das Schleifen wurde in zwei Arbeitsschritte aufgeteilt: Zuerst erfolgte der Anschliff auf der Unterseite der Sense. Der Anschleifer stand dafür an einem großen Schleifstein und arbeitete in gebückter Haltung. Danach wurde die Oberseite scharfgeschliffen. Dafür setzte sich der Scharfschleifer rittlings auf einen Holzbalken vor einen kleineren Schleifstein. In vorgebeugter Haltung drückte er die Oberseite der Sense gegen den rotierenden Schleifstein. Bei beiden Arbeitsschritten wurden die Schleifsteine aus Naturstein durchgängig mit Wasser berieselt. Das führte zur Rostgefahr an den Sensen. Sie wurden deshalb in ein Bad mit chemischem Rostschutzmittel getaucht. Damit das Rostschutzmittel richtig einwirkte, wurden die Sensen im Trockenofen getrocknet.
Die unnatürliche gebückte Haltung, der feine Staub, der beim Schleifen entsteht, die dauerhafte Lärmbelastung durch die rotierenden Schleifsteine, die Nässe und das kräftezehrende Halten der Werkstücke führten zu Gesundheitsschäden: Haltungsschäden, rheumatischen Erkrankungen, Magenbeschwerden, Lärmschwerhörigkeit und Atemwegs- und Lungenerkrankungen.
Beteiligte Berufe:
- Anschleifer: Arbeiten in einem Sensenhammer und haben sich auf den Anschliff der Sensen spezialisiert. Sie bearbeiteten die Unterseite der Sensenblätter.
- Scharfschleifer: Arbeiten in einem Sensenhammer und haben sich auf den Scharfschliff der Sensen spezialisiert. Sie bearbeiteten die Oberseite der Sensenblätter.
Endbearbeitung
Polieren und Dengeln
Nach dem Schleifen wurden die Sensen vom Polierer an den Polierscheiben auf Hochglanz gebracht. Je nach Sensensorte gab es Abstufungen im Glanz. So waren die Reichsformsensen meist beidseitig hochglänzend poliert. Andere Formen waren nur einseitig poliert, geschrappt oder schnittpoliert.
Es folgte das Dengeln der Schneide, die mit einem meißelartigen Obersattel (quasi dem Hammer) final geschärft wurde. Jetzt besaßen die Sensen die vorgeschriebene Schärfe.
Beteiligte Berufe:
- Polierer: Arbeitet im Sensenhammer und hat sich auf die Politur von Sensenblättern spezialisiert.
- Dengler: Schmied im Sensenhammer, der der geschliffenen Schneide den letzten Schliff verpasst und somit für die geforderte Schärfe sorgt.
Ziertupfen und Nachrichten
Nach dem Dengeln besaßen die Sensen zwar die vorgeschriebene Schärfe, hatten aber leicht an Spannung verloren. Daher wurden sie nun noch einmal durch das Ziertupfen „auf Spannung“ gebracht und stabilisiert. Der verzierende Nebeneffekt war verkaufsfördernd.
In der Richterei wurde noch einmal nachgerichtet und verbliebene Unebenheiten ausgeglichen. Diese abschließende Qualitätskontrolle wurde von einem sehr erfahrenen Schmied ausgeführt, dem Nach- oder Feinrichter.
Beteiligte Berufe:
- Nachrichter: Schmied im Sensenhammer, der sich auf das Feinrichten der fertigen Sensen als abschließende Qualitätskontrolle spezialisiert hat.
Lackieren und Ausstatten
Nach der Qualitätskontrolle wurden die Sensen an Rücken und Hamme in der Lackiererei mit farbigen Lacken versehen, um die einzelnen Sorten unterscheiden zu können. Zuletzt erhielten alle Sensen einen Rostschutzlack. Nun wurden auch Etiketten mit den einzelnen Markennamen aufgeklebt.
Verpacken und Wiegen
12 oder 13 Sensen wurden zu einem Bunde zusammengepackt und zu den gewünschten Kundenkommissionen zusammengestellt, gewogen, verpackt und versendet.
Für Transporte der scharf geschliffenen Sensen eigneten sich Fässer besonders gut. Sensen wurden zu 12 oder 13 Stück gebündelt und in Langstroh gewickelt. Das Stroh verhinderte, dass die Sensen sich gegenseitig beschädigten. Die schweren Fässer konnten gerollt werden. Erst Ende der 1930er-Jahre setzten sich Kisten als Verpackungsmaterial für Sensen durch.
Literatur
- Margarete Asbeck: Die Sensenindustrie an der Ennepestrasse. Haspe 1923.
- Wolfgang Fach (Hg.): Die ganze Welt ist unser Feld. Reclame-Kunst um 1900 der Ausrüster für das Graphische Gewerbe. Frankfurt a. M. 1985.
- Kai Lohsträter: Letzte Zeugen. Zur Geschichte des Ennepetaler Sensenwerks und der Sensenherstellung in Südwestfalen. In: TKD 47/2007, S. 4–7.
- Kerstin Schumann: Die Sensenindustrie der Enneperstr. In: Vom heißen Eisen. Hagen 1993, S. 133-146.
Weiterführende Links
- YouTube - https://www.youtube.com/watch?v=_Iiynm-i5UU
- Freudenthaler Sensenhammer - https://www.sensenhammer.de/
Machen Sie mit! Teilen Sie Ihr Wissen mit uns!
Machen Sie mit
Bringen Sie sich ein mit Ihrem Wissen und halten Sie so das das handwerkliche Erbe Westfalen-Lippes lebendig! Hier finden Sie alle Aktionen.
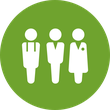
Schreiben Sie uns
LWL-Freilichtmuseum Hagen
Kompetenzzentrum Handwerk und Technik
Mäckingerbach · 58091 Hagen
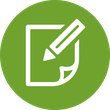
Schicken Sie uns eine E-Mail
Sie möchten Ihre Erfahrungen und Ihr Wissen mit uns teilen? Schicken Sie uns eine E-Mail – wir freuen uns auf Ihre Nachricht!
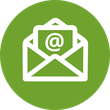
Rufen Sie uns an
Sie erreichen uns von Montag bis Donnerstag von 9 bis 16 Uhr und Freitags von 9 bis 13 Uhr.
Tel: 02331 7807-177
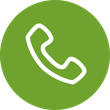
Film ab!
Über 70 Videos und kurze Filme gibt es auf dem YouTube-Kanal des Museums. Reinschauen lohnt sich!
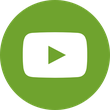
Folgen Sie uns
Bildgewaltig! Die aktuellsten Fotos und Meldungen aus dem Museum. Abonnieren nicht vergessen!
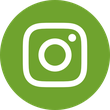